Systematic fatigue research dates back to the mid-1800s and fatigue analysis and prevention is nowadays one of the basic elements of machine and structural engineer’s studies. One could therefore think that material fatigue is a thing of the past, i.e., a challenge that has been solved a long time ago. Unfortunately not! Material fatigue involves numerous aspects that vary from case to case in a manner that is very challenging to predict in advance. Furthermore, fatigue is a “weakest link” -type phenomenon, that is, even if the loaded part is 99.999% pristine, the remaining 0.001% with undesired properties may eventually lead to fatigue failure of the whole part. This contrasts with many other mechanical material properties, such as stiffness, which typically represent an average of the volume in question.
The demands on the performance of structures and machinery are ever increasing which naturally increases the demands on material performance. One interesting way to tackle these challenges is to use “hybrid materials” i.e., combinations of two or more materials from different material groups. The hardmetal coatings overlaid on a high strength steel substrate studied in the PerforMat project are one interesting example of such a material combination; it offers a good combination of structural strength (from the steel substrate) with high surface hardness and wear resistance (from the hardmetal coating). However, in terms of fatigue performance, the analysis of this kind of a “material system” is challenging and multifaceted, as illustrated schematically by Figure 1. For example, the involved materials have very different microstructures and inherent mechanical properties. Furthermore, some properties of this material system, such as the behavior of the material interface and the residual stress state in the different parts of the system, are specific to the combination at hand and the manufacturing process. Experimental fatigue testing and analysis is therefore paramount for the successful use of these materials in demanding applications.
The work carried out in PerforMat WP2/Use Case 1 is concentrating on the analysis of fretting behavior of hardmetal coating/steel substrates. Fretting is a phenomenon that causes damage on different kinds of load carrying contacts, such as those found in mechanical joints. The root cause for fretting is micrometer scale reciprocating slip between the contact surfaces under the influence of tangential forces created by friction. Depending on the case, fretting damage can manifest itself as wear of the surface(s) or formation of a fatigue crack (or the combination of both). In the case of coating/substrate-pairs understanding fretting behavior is important because the loads imposed on the material during fretting act on and just below the contact surface, i.e., there where the two very dissimilar materials (coating and substrate) meet!
More information on the fretting and fatigue research at TAU can be found at https://www.tuni.fi/en/research/tribology-and-machine-elements
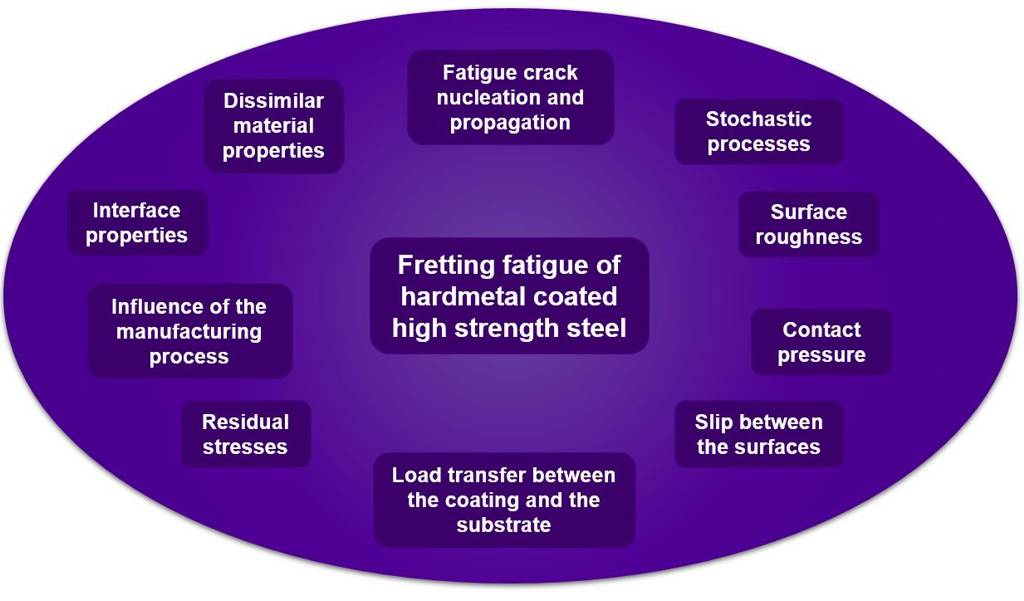